產品目錄
產品一覽
- 壓縮空氣管理系統
- 方向控制元件
- 氣壓缸
- 旋轉缸/氣壓夾爪
- 電動驅動器/單軸機器人
- 真空設備(真空發生器/真空吸盤/其他)
- 協作機械手臂用 真空夾取單元 (zh-tw)
- Compact Compressor (zh-tw)
- 壓縮空氣清淨化元件
- 模組型F.R.L./壓力控制元件
- 模組型F.R.L (zh-tw)
- 壓力控制元件 (zh-tw)
- 增壓缸
- 潤滑元件
- 接頭&氣壓管
- 流量控制元件
- 消音器/油霧回收器/空氣噴槍/壓力錶
- 開關/感測器/控制器
- 靜電消除器
-
產業用通訊元件/無線系統
- Wireless System: PROFINET Compatible Products
- Wireless System: EtherNet/IP Compatible Products
- Wireless System: EtherCAT Compatible Products
- Wireless System: IO-Link Compatible Products
- Wireless System: CC-Link Compatible
- Wireless System: DeviceNet Compatible Products
- Industrial Device Communication Equipment: PROFINET Compatible Products
- Industrial Device Communication Equipment: EtherNet/IP Compatible Products
- Industrial Device Communication Equipment: EtherCAT Compatible Products
- Industrial Device Communication Equipment: Modbus TCP Compatible Products
- Industrial Device Communication Equipment: ETHERNET POWERLINK Compatible Products
- Industrial Device Communication Equipment: CC-Link IE Field Compatible Products
- Industrial Device Communication Equipment: SSCNET III Compatible Products
- Industrial Device Communication Equipment: MECHATROLINK-Ⅲ Compatible Products
- Industrial Device Communication Equipment: PROFIsafe Compatible Products
- Industrial Device Communication Equipment: IO-Link Compatible Products
- Industrial Device Communication Equipment: PROFIBUS Compatible Products
- Industrial Device Communication Equipment: DeviceNet Compatible Products
- Industrial Device Communication Equipment: CC-Link Compatible Products
- Industrial Device Communication Equipment: AS-interface Compatible Products
- Industrial Device Communication Equipment: CANopen Compatible Products
- Industrial Device Communication Equipment: CompoNet Compatible Products
- Industrial Device Communication Equipment: Interbus Compatible Products
- Industrial Device Communication Equipment: MECHATROLINK-Ⅱ Compatible Products
- Other: RS232C Compatible Products
- Other: RS485 Compatible Products
- Wireless System: PROFINET Compatible Products
- 流體閥
- 藥液用閥/接頭&針閥/配管
- 製程幫浦(膜片式幫浦)
-
恆溫元件
- 恆溫器 (循環液恆溫裝置)Standard Type/Basic Type zh-tw
- 恆溫器 (循環液恆溫裝置)Inverter Type zh-tw
- 恆溫器 (循環液恆溫裝置)Dual Channel Thermo chiller for Lasers zh-tw
- 恆溫器 (循環液恆溫裝置)Rack Mount Type zh-tw
- 恆溫器 (循環液恆溫裝置)High performance/Type & Inverter Type zh-tw
- 恆溫器 (循環液恆溫裝置)
- Chiller Compliant Regulations
- 致冷晶片式恆溫器/恆溫槽 (致冷晶片式恆溫裝置)
- 空冷式恆溫機
- 恆溫器 (循環液恆溫裝置)Standard Type/Basic Type zh-tw
- 製程氣體用元件
- 高真空元件
- 工業用過濾器/燒結金屬濾芯
- 計裝用補助元件
- 油壓元件
按主題/行業分類的目錄
協作機械手臂用 真空夾取單元
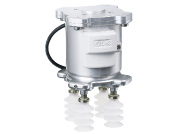
Vacuum Gripper for Collaborative Robots ZXP7□21-X1
for the FANUC CORPORATION CRX Series
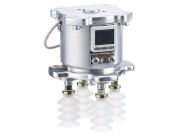
Vacuum Gripper for Collaborative Robots ZXP7□-X1□-KA
for the Kawasaki Heavy Industries, Ltd. duAro 1, 2 Series
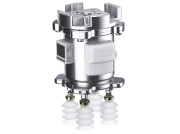
Vacuum Gripper for Collaborative Robots ZXP7□-X1□-ASSISTA
for Mitsubishi Electric Corporation MELFA ASSISTA
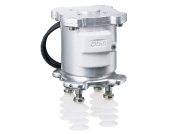
Vacuum Gripper for Collaborative Robots ZXP7□41-X1
for the OMRON Corporation and TECHMAN ROBOT Inc. TM Series
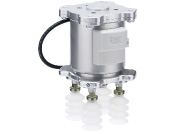
Vacuum Gripper for Collaborative Robots ZXP7□01-X1
for Universal Robots
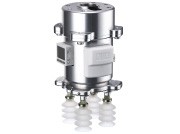
Vacuum Gripper for Collaborative Robots ZXP7□11-X1□
for YASKAWA Electric Corporation collaborative robot MOTOMAN-HC10DT
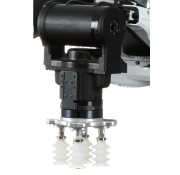
Cups with Flange for Collaborative Robots ZXP7-PFL1-□-X1
for KAWADA ROBOTICS CORPORATION, NEXTAGE
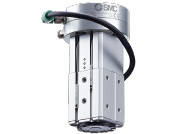
Magnet Gripper for Collaborative Robots MHM-X7400A-CRX
for the FANUC CORPORATION CRX Series
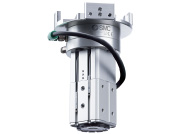
Magnet Gripper for Collaborative Robots MHM-X7400A-ASSISTA
for the Mitsubishi Electric Corporation MELFA ASSISTA Series
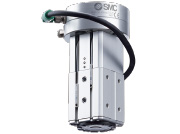
Magnet Gripper for Collaborative Robots MHM-X7400A-TM
for the OMRON Corporation and TECHMAN ROBOT Inc. TM Series
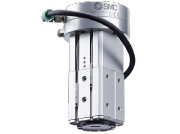
Magnet Gripper for Collaborative Robots MHM-X7400A
for Universal Robots
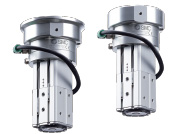
Magnet Gripper for Collaborative Robots MHM-X7400A-HC10/HC10DT
for the YASKAWA Electric Corporation MOTOMAN-HC